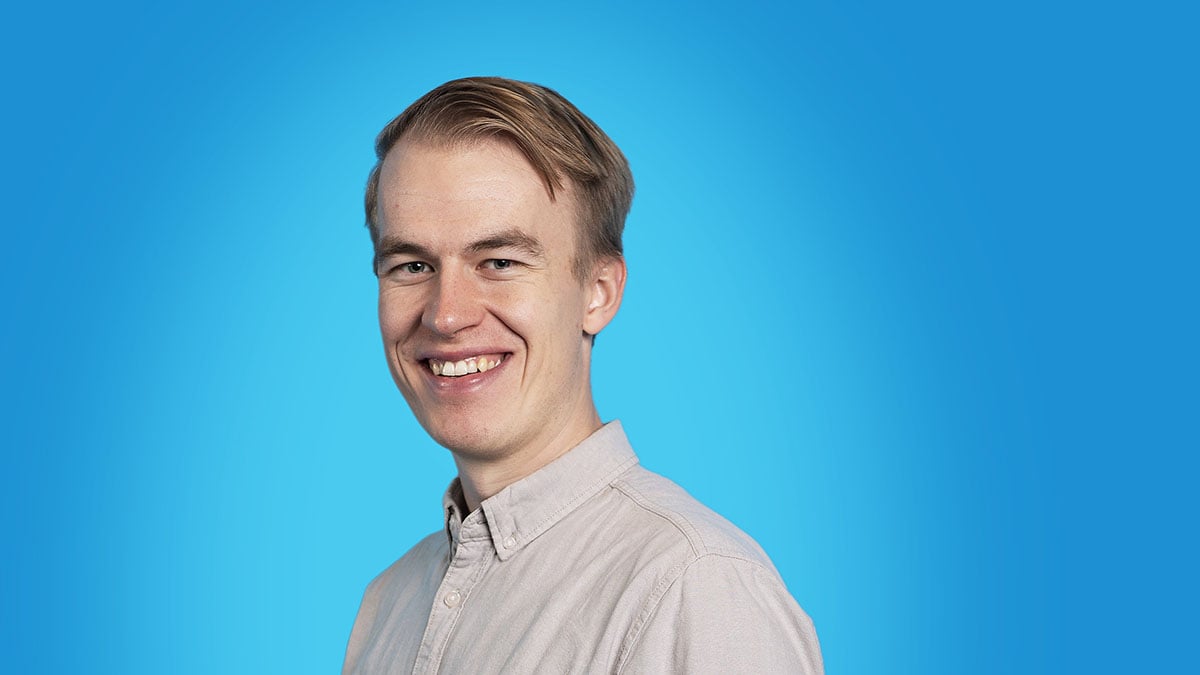
Helen simulates hydrogen production with a digital twin
Simulating hydrogen production reveals potential deficiencies and malfunctions in automation systems, which smoothens the commissioning of the hydrogen plant. The digital twin of the hydrogen plant enables automated hydrogen production and its optimisation during the plant's production phase.
Helen's entry into the renewable hydrogen market progresses as the construction of the first hydrogen production plant in Helsinki, the 3H2 Helsinki Hydrogen Hub, begins in the coming weeks. The plant will produce hydrogen with renewable electricity for transportation and industrial consumption. Renewable hydrogen can be used to replace fossil fuels either directly or indirectly, reducing emissions in sectors where emission reductions have not yet advanced significantly.
From Helen's point of view, the 3 MW project is larger than its size as it serves as an educational institution for the organization to familiarise itself with hydrogen production technology, markets, and new business models. The pilot plant lays a stable foundation for the commissioning of significantly larger renewable hydrogen production facilities in the future.
Virtual commissioning reduces risks
Funded by the European BalticSeaH2 project, Helen aims to create new digital capabilities around the new business area. Using Siemens’ software, a simulation of the production process of the 3H2 hydrogen plant will be built. By utilising the simulation, a virtual commissioning of the plant and its automation systems will be conducted during the plant's Factory Acceptance Testing. The virtual commissioning is carried out together with automation suppliers, improving the testing possibilities of automation and smoothing the actual commissioning phase.
Virtual commissioning tackles challenges that often arise in the commissioning of complex processes. Testing in a digital environment that mirrors the real-world enables more comprehensive and high-quality automation development. In addition, testing can continue if deficiencies or incorrect functions in automation are observed during the commissioning. Generally, the need for changes during the commissioning phase can cause significant delays and additional costs. The main purpose of virtual commissioning is to reduce these risks.
The digital twin creates a competitive advantage
After virtual commissioning, the simulation and tested automation systems are integrated into Helen's production management systems. The goal is to operate the simulated plant automatically and flexibly, optimising hydrogen production based on energy system and market conditions. In this scenario, the simulation can be utilised as a so-called digital twin alongside the real plant. The digital twin enables continuous analysis and development of operational activities without disrupting production.
Hydrogen production by electrolysis is an established technology and there is ample experience with it. However, the investments in renewable hydrogen production required for the clean transition as well as the pressure created by increased renewable electricity production capacity for flexible electricity consumption pose entirely new challenges. Building the aforementioned digital capabilities can give Helen a significant competitive advantage in developing hydrogen markets.